Design for Manufacture has taken on a whole new direction. It used to be enough to consider component spacing, orientation, and electronic compatibility. The number of components used in electronic products today has increased significantly, therefore putting a strain on the availability of components in the market place.
MOORE’S LAW
Gordon Moore, Co-Founder of Intel authored Moore’s Law in 1965 – Moore states that the number of components able to fit on a single IC will double every year. In 1985 Moore tweaked his projection to read “doubling every 2 years”. This has continued to hold true for over 30 years. Some say this is coming to an end as components will only get so small; however, the demand for new electronic devices continues to rise adding to the strain on the component supply. The incredible increase in usage – demand outpacing supply, sourcing of raw materials, dealing with trade agreements and tariffs are lengthening our lead times considerably.
A GAME CHANGER
These days the strained availability of components make it a whole new game. Component size has decreased significantly allowing many more parts to be placed within the footprint of today’s smaller electronic devices. The concept of Design for Manufacturability is joined by the necessity of Design for Availability.
Everyone can relate to the general consumer example of the cell phone. Using today’s smaller component package size, mobile devices have decreased in size with a significant increase in functionality. The capability of today’s integrated circuits turns cell phones into mini-computers with email, camera, video, internet access and thousands of apps making today’s product much different than Motorolas’ DynaTAC launched commerically in 1984 with 30 minutes of talk time. This remarkable evolution is also evident in many other products including automobiles, medical devices, commercial and industrial equipment, consumer devices and aerospace applications.
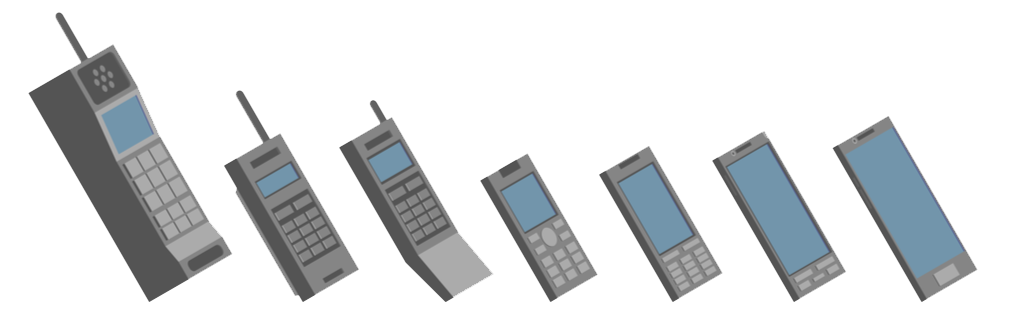
1983 – Motorola Dynatac 8000X weighed – 1.75 pounds and was 13″ x 1.75″ x 3.5″.
2018 – iPhone XS Max weighs 7.34 oz and is 3″ x 6.25″ x .33″.
WHAT YOU CAN DO
Design Engineers many not have control over the component market, but there are some things we can do to avoid shutting down assembly lines.
• Use smaller packages where possible. For example, replace 1206 and 0805 chip caps and resistors with 0603, 0402, and 0201.
• Verify that specified parts have an active lifecycle status (instead of Not Recommended for New Design, End of Life, etc.).
• Spec at least 3 alternates for each item on the BOM, with a different manufacturer for each.
• Use the lowest rating and widest tolerance range your design can handle. If these parts become unavailable, the same part with a tighter tolerance or higher rating may still be available.
TEAM UP WITH YOUR CM
We’re here to be a part of your solutions team. Getting your CM involved early in the process will add significant value and eliminate build delays. Altek can often assist with recommendations for alternates or suggest custom solutions. We will identify and can handle advance ordering on long lead items. Our excellent relationships with our distributors give us an edge in meeting your needs.
THE MORAL OF THE STORY
As Ben Franklin said in 1736 “An ounce of prevention is worth a pound of cure”. This still holds true today. Design for Availability activities will mitigate lead times and get your product to market on time.